The manufacturing industry has witnessed numerous advancements over the decades, but few processes have revolutionized production as much as family mold injection molding. This process has become indispensable for creating multiple related parts efficiently within a single mold. With applications in industries ranging from automotive to electronics, it has become a cost-effective and highly efficient production method. This article provides a detailed exploration of family mold injection molding, its advantages, challenges, and its growing presence in China.
What is Family Mold Injection Molding?
Family mold injection molding is a specialized manufacturing technique that allows multiple different components to be produced in a single mold. These components, often related or complementary, are molded simultaneously, making it easier to assemble final products. For example, in an automotive assembly, different parts such as buttons, frames, and covers can be manufactured together, reducing costs and time.
The mold consists of multiple cavities, each shaped for a specific component. During the injection process, molten plastic is injected into these cavities simultaneously. Once cooled, the parts are ejected together, ready for further processing or assembly. This approach simplifies production, improves efficiency, and reduces material wastage.
In industries requiring high-volume production, family mold injection molding ensures consistent quality across all components, as they are molded under identical conditions.
The Importance of Family Tool Injection Molding
A critical aspect of this process is the tooling design, often referred to as family tool injection molding. The tool, or mold, must be designed with precision to ensure uniform filling, cooling, and ejection of all parts.
Family tool injection molding involves creating cavities that can accommodate parts of different sizes and complexities. Engineers carefully analyze the flow of molten plastic to ensure even distribution. Any imbalance in the design can result in defects like incomplete filling or warping.
The tooling process also takes into account the ease of assembly, ensuring that all parts align perfectly after molding. This makes it especially useful in industries requiring tightly fitting components, such as electronics and medical devices.
The Process of Family Mold Injection Molding
The family mold injection molding process begins with designing the mold based on the required components. Engineers consider factors such as part geometry, material type, and expected production volumes.
Once the mold is designed, it is fabricated using steel or aluminum. The mold is then mounted onto an injection molding machine, which injects molten plastic into the cavities under high pressure.
Key steps in the process include:
- Clamping – The mold is securely closed and prepared for injection.
- Injection – Molten plastic is injected into the mold under high pressure, ensuring it fills all cavities.
- Cooling – The plastic cools and solidifies inside the mold.
- Ejection – The molded parts are ejected from the mold and prepared for post-processing, if required.
This process can produce thousands of parts in a short timeframe, making it highly efficient for mass production.
Applications of Family Mold Injection Molding
Family mold injection molding is widely recognized for its adaptability and efficiency across multiple industries. Its ability to produce multiple components simultaneously within a single mold makes it ideal for manufacturing complex assemblies. This technique is particularly beneficial for industries that require high precision, uniformity, and cost-effective production. From automotive components to medical devices, family mold injection molding continues to play a critical role in modern manufacturing.
Automotive Industry
The automotive industry is one of the largest consumers of family mold injection molding due to its demand for precision parts that need to fit seamlessly within intricate assemblies. Automakers often require multiple plastic components, such as dashboard panels, buttons, knobs, trims, and handles, which can be produced simultaneously using family molds. This process is not only cost-effective but also ensures consistency in quality, which is essential for vehicle interiors and mechanical parts.
For example, a car’s dashboard might require different components—such as vents, control panels, and instrument housings—that need to be manufactured with exact dimensions. By utilizing family mold injection molding, manufacturers can produce these parts in one cycle, saving time and labor costs. The process also supports overmolding, which allows manufacturers to combine soft-touch materials with hard plastic components, enhancing durability and aesthetics.
Moreover, automotive manufacturers often require parts made from high-performance plastics that can withstand heat, pressure, and wear. Family tool injection molding enables them to produce such components with uniform mechanical properties, ensuring reliability and long-term performance. With the growing popularity of electric vehicles, the demand for lightweight plastic components has further boosted the adoption of this technology, making it a cornerstone of automotive manufacturing.
Consumer Electronics
In the consumer electronics industry, family mold injection molding is indispensable for creating compact, lightweight, and durable parts. Devices such as mobile phones, remote controls, gaming consoles, and smart home gadgets consist of multiple plastic parts that must fit perfectly during assembly. The ability to produce these parts in a single mold simplifies production, reduces costs, and ensures dimensional accuracy.
For instance, a television remote control requires buttons, housing shells, and battery covers—all of which can be manufactured together using family molds. Similarly, smartphones often require frames, back covers, and button panels that must be produced with precise measurements and finishes. Family tool injection molding makes it possible to mold these parts together, ensuring compatibility and structural integrity.
In addition to traditional plastics, overmolding is frequently used in this sector to add rubberized grips, protective coatings, or transparent windows to plastic parts. This improves the functionality and visual appeal of electronic products. Manufacturers in injection mold China are leading the charge in providing high-precision molds for consumer electronics, further solidifying China’s role as a global leader in this industry.
Medical Devices
The medical industry relies heavily on family mold injection molding for producing highly precise and sterile components. Medical devices often consist of multiple interconnected parts, such as syringes, diagnostic kits, enclosures, and surgical instruments, which must meet strict safety and quality standards. Family molds allow manufacturers to produce these components simultaneously, ensuring consistency and compliance with regulatory requirements.
For example, a syringe consists of a barrel, plunger, and needle cap—each requiring exact dimensions to function correctly. Using family molds, all these parts can be manufactured in a single process, maintaining uniform quality and reducing assembly errors. This is particularly important in medical applications, where even minor defects can compromise patient safety.
Additionally, plastic mold materials used in medical devices often require biocompatibility, chemical resistance, and sterilization capabilities. Family molds can handle specialized plastics like polycarbonate and polyethylene, which are commonly used in healthcare products. Leading plastic injection molding companies are equipped with cleanroom facilities to ensure contamination-free production, meeting the rigorous standards of the medical sector.
Household Products
Household products represent another significant area where family mold injection molding is widely used. From kitchen utensils and storage containers to decorative items and furniture parts, this method allows manufacturers to produce multiple components simultaneously, reducing costs and production times.
For example, a kitchen appliance like a blender may require buttons, knobs, lids, and base covers. Instead of manufacturing these parts separately, family tool injection molding allows manufacturers to mold them together, ensuring compatibility and consistent quality. This approach is particularly advantageous for products with modular designs, as it reduces assembly requirements and simplifies inventory management.
Household items often require visually appealing finishes and ergonomic designs, which can be achieved through overmolding techniques. Rubberized handles, transparent lids, and textured surfaces can be added seamlessly during the molding process. This makes products more functional and aesthetically pleasing while maintaining durability.
Manufacturers in mold factories in China excel in producing molds for household items, leveraging advanced technologies and cost-effective processes. Their ability to deliver customized designs and high-volume production has made them preferred partners for global brands.
Other Industries Benefiting from Family Mold Injection Molding
Apart from the major sectors mentioned above, family mold injection molding is also widely used in other industries, such as:
- Toys and Games – Produces various parts for puzzles, figurines, and board games in one production cycle.
- Packaging Industry – Used for creating lids, closures, and containers for food and beverages.
- Aerospace Industry – Manufactures lightweight and durable components for aircraft interiors.
- Construction Materials – Produces tools, connectors, and fittings required for building infrastructure.
Each of these industries benefits from the cost efficiency, precision, and scalability offered by family mold injection molding.
The Growing Role of China in Family Mold Injection Molding
China has emerged as a global leader in family mold injection molding, providing affordable and high-quality solutions to businesses worldwide. Mold factories in China are equipped with state-of-the-art machinery and experienced engineers, making them ideal partners for both prototyping and large-scale production.
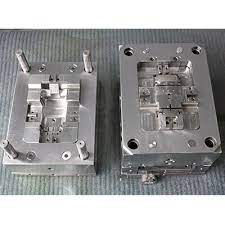
Chinese manufacturers are also leading in innovations such as die casting China and die casting mold technologies, which complement plastic injection molding for creating hybrid products. These advancements have expanded the possibilities for manufacturers looking to integrate metal and plastic components into single assemblies.
Companies specializing in injection mold China also offer flexible services, including rapid prototyping, small-batch production, and customized mold designs. Their ability to provide end-to-end solutions makes them a reliable choice for businesses across industries.
China’s Role in Family Mold Injection Molding
China has established itself as a global hub for family mold injection molding. The country’s advanced infrastructure, skilled workforce, and competitive pricing have made it a preferred destination for mold manufacturing.
Many plastic injection molding companies in China specialize in creating molds tailored to clients’ specific needs. With access to cutting-edge technology, these companies offer services ranging from prototyping to large-scale production.
Chinese manufacturers excel in producing plastic mold tools, ensuring high precision and durability. Their expertise in injection mold China production has positioned them as leaders in the industry.
The availability of mold factories in China further enhances production capabilities, allowing companies to scale operations efficiently.
Key Benefits of Family Mold Injection Molding
- Cost Savings – Producing multiple parts in one mold reduces tooling costs and operational expenses.
- Time Efficiency – Simultaneous production of parts accelerates manufacturing timelines.
- Consistency – Parts molded together share identical material properties and finish quality.
- Flexibility – Allows production of parts with different shapes and sizes in the same mold.
- Material Optimization – Reduces waste by utilizing raw materials more efficiently.
The process also supports overmolding, enabling manufacturers to combine materials for improved functionality.
Challenges in Family Mold Injection Molding
Family mold injection molding offers numerous advantages, but like any manufacturing process, it also presents distinct challenges that manufacturers must address to ensure optimal performance and efficiency. These challenges primarily revolve around design complexities, uniform filling, maintenance issues, and higher initial costs. Tackling these challenges requires a combination of advanced engineering, precise planning, and collaboration with experienced plastic injection molding companies to deliver consistent results.
Design Complexity
Designing family molds is a highly intricate process that demands exceptional engineering expertise. Since family mold injection molding involves creating multiple cavities within a single mold, these cavities must be carefully balanced to accommodate different component sizes, shapes, and volumes. Each cavity needs to be designed to ensure that molten plastic flows uniformly and fills every section completely. If one cavity is larger or smaller than others, it can lead to uneven filling, resulting in defective parts such as short shots or flash. Furthermore, variations in wall thickness among the parts can cause differences in cooling rates, potentially leading to warping or shrinkage. Engineers must meticulously calculate dimensions and flow rates, often utilizing advanced software for mold flow analysis to simulate the injection process before mold fabrication begins. Any errors in design can lead to costly revisions and delays, emphasizing the need for expertise in family tool injection molding.
Uniform Filling and Balancing the Mold
Achieving uniform filling is another major challenge in family mold injection molding. The process requires molten plastic to be injected into multiple cavities simultaneously, but parts with different volumes or dimensions can lead to imbalances in pressure and flow rates. If one cavity fills faster than another, it can create defects such as voids, sink marks, or incomplete fills. Engineers address this issue by designing balanced runners and gates to control the flow of plastic and maintain equal pressure throughout the mold. Specialized gating systems, such as hot runners, are often employed to improve balance and reduce material waste. However, implementing these systems can increase the initial tooling costs, requiring careful budget planning. For this reason, partnering with experienced plastic injection molding companies ensures proper mold design and testing to prevent such issues during production.
Maintenance Issues and Wear Variability
Mold maintenance is a critical aspect of sustaining quality and efficiency in family mold injection molding. Since different cavities within the mold may experience varying levels of wear and tear, maintaining uniform performance becomes challenging over time. Larger cavities or those with intricate designs may be subjected to higher pressures, leading to faster degradation compared to simpler cavities. Regular inspection and maintenance routines are essential to identify and address early signs of damage, such as cracks, corrosion, or misalignment. Replacing or repairing specific cavities can be time-consuming and expensive, especially if the mold design does not allow for modular replacements. Working with a mold factory in China can help alleviate some of these challenges, as Chinese manufacturers are known for offering durable molds and cost-effective maintenance services. Advanced monitoring systems and sensors are also being integrated into modern molds to track performance metrics and predict maintenance requirements, reducing unexpected downtime.
Higher Initial Costs for Tooling and Fabrication
One of the most significant barriers to adopting family mold injection molding is the higher initial investment required for tooling and fabrication. Designing and producing a multi-cavity mold involves complex engineering and precise machining, leading to increased upfront costs compared to single-cavity molds. The addition of features such as balanced runners, hot runners, and specialized cooling systems further contributes to the overall expense. However, these initial costs are often offset by long-term savings in production efficiency, reduced labor costs, and minimized material waste. Businesses looking to adopt this method often collaborate with manufacturers specializing in injection mold China to keep tooling costs within budget. Chinese manufacturers have established themselves as global leaders in cost-effective mold production without compromising quality, making them an attractive option for businesses worldwide.
Addressing the Challenges Effectively
Overcoming these challenges requires a multi-pronged approach that combines engineering innovation, process optimization, and regular quality control. Collaborating with reputable plastic injection molding companies provides access to advanced technologies, experienced design teams, and comprehensive testing facilities. Additionally, leveraging software tools like CAD/CAM for mold design and flow simulation can reduce errors and enhance precision. Manufacturers also benefit from working with mold factories in China, which offer competitive pricing and fast turnaround times for both prototyping and large-scale production. By integrating these strategies, businesses can effectively address the complexities of family tool injection moldingand ensure high-quality results.
The Role of Advanced Technologies in Overcoming Challenges
To further address the challenges associated with family mold injection molding, manufacturers are increasingly adopting advanced technologies like automation, robotics, and artificial intelligence. Automation helps streamline repetitive tasks such as mold clamping and part ejection, improving efficiency and reducing human errors. Robotics assist in material handling and quality inspections, ensuring consistent output. AI-driven systems enable predictive maintenance by monitoring the performance of molds and identifying potential defects before they escalate. These technologies are particularly popular in mold factories in China, where large-scale production demands high precision and efficiency.
Another innovation that is gaining traction is overmolding, which allows manufacturers to produce complex parts by molding multiple materials together. This process is often integrated with family mold injection molding to create parts with enhanced strength, flexibility, and aesthetics. For example, in consumer electronics, overmoldingis used to add rubberized grips to plastic enclosures, improving durability and user experience. Similarly, advancements in die casting China and die casting moldtechnologies are complementing traditional injection molding methods, enabling manufacturers to combine plastic and metal components within a single mold.
Practical Solutions for Cost Management
Managing costs effectively is crucial for businesses considering family mold injection molding. While the initial investment in tooling and design can be high, adopting lean manufacturing principles helps minimize material waste and optimize production cycles. Businesses often turn to injection mold China manufacturers to benefit from lower labor costs and advanced equipment. Additionally, bulk orders and long-term partnerships with mold factories in China can lead to volume discounts, further reducing expenses.
Investing in modular mold designs also provides cost benefits by allowing manufacturers to replace individual components rather than redesigning the entire mold. This approach enhances flexibility and extends the lifespan of the mold, leading to better returns on investment.
Future Trends in Injection Molding
The future of family mold injection molding is being shaped by advancements in automation, robotics, and die casting China technologies. Modern machines are now equipped with sensors and monitoring systems that enhance precision and reduce errors.
China’s die casting mold expertise is also contributing to innovations in hybrid manufacturing, where plastic and metal components are combined in the same mold.
Additionally, the integration of smart technologies is enabling manufacturers to track performance in real time, ensuring better quality control and faster production cycles.
How to Choose the Right Mold Factory in China
Selecting the right mold factory in China is crucial for achieving high-quality production. Factors to consider include:
- Experience and Expertise – Assess the factory’s track record in family mold injection molding projects.
- Technology and Equipment – Ensure they use the latest machinery and tools.
- Certifications – Check for compliance with international standards and certifications.
- Customer Support – Reliable after-sales service and technical support are essential for long-term success.
Companies involved in die casting China and injection mold China also often provide custom tooling solutions, ensuring compatibility with diverse production needs.
Conclusion
Family mold injection molding has transformed the manufacturing landscape by offering cost-effective, high-precision solutions for producing multiple components simultaneously. Its ability to streamline production processes and reduce costs has made it a popular choice in industries worldwide.
With China leading the way in this technology, businesses have access to reliable and affordable manufacturing solutions. From plastic mold tools to die casting mold designs, the opportunities for innovation and scalability are vast.
For businesses looking to optimize production, embracing family tool injection molding is a step toward greater efficiency and profitability.