In the machining manufacturing process, computer numerical control (CNC) machining uses numerical controls to regulate cutting tool movement. It helps to produce a range of CNC machining parts with either simple or complex geometries depending on degree of complexity. One of the factors influencing the change of the manufacturing sector is this technology. Previously challenging, it has made it far easier to create complex parts with higher accuracy. Your only need is to draw your ideas down on a sheet of paper; the machines will take care of everything else.
Let’s review CNC parts, learn how you could choose the best ones, and talk about the benefits of employing those parts.
Unlike other techniques, CNC machining
With numerical controls, CNC machining is a production technology that controls cutting tool movement. It helps to produce CNC parts with either simple or sophisticated geometry. This technology is altering manufacturing. It has streamlined and raised the precision of producing difficult parts. The machines will handle everything; you just need to jot your ideas on paper.
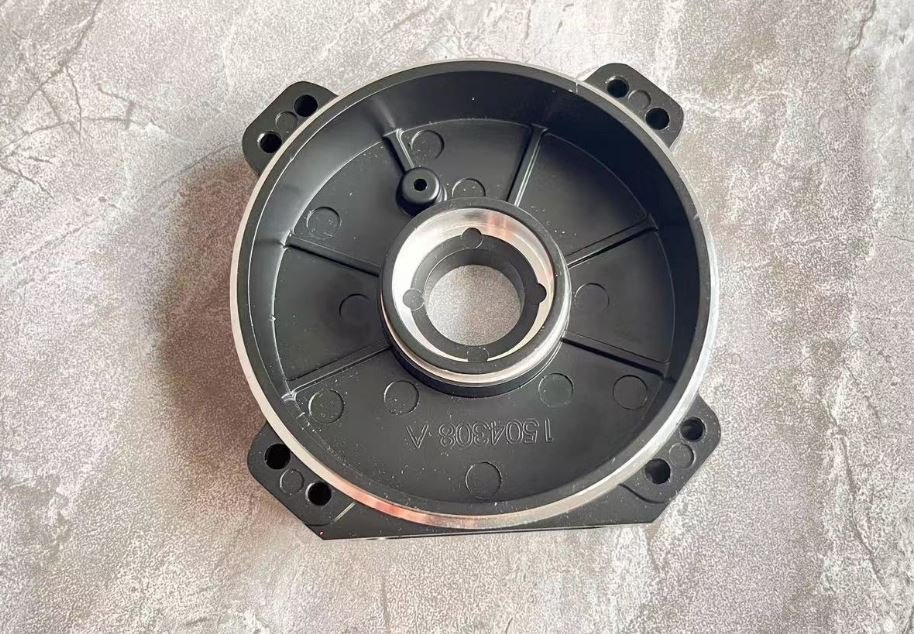
Qué es el mecanizado CNC de piezas
The components that have been manufactured via the use of the CNC machining method are referred to as having CNC machining parts. Without a doubt, you are curious about the nature of this method. It requires the utilization of various cutting machines and tools, including mills, lathes, and grinders, among others. The production of a desired component of a piece of machinery is the ultimate objective. Even though the operating mechanism of each of these devices is distinct from one another, they all accomplish the same thing.
There are two distinct forms of CNC machining, each of which operates differently. A part can be brought into the correct shape and size by the process of manual machining, which requires the use of tools that are operated manually. Alternatively, there is another method, which is known as digital machining. It makes use of instructions that have been pre-programmed and that you feed into the devices. They carry out their operations in accordance with such parameters. You end up with machined parts that are accurate, consistent, and effective as a consequence.
Within the context of this technique, there are no such restrictions imposed on the utilisation of resources. These materials consist of ceramics, metals, and polymers. On the other hand, before deciding on the material, you need to take a few things into consideration. Considerations like as cost, conductivity, resistance, and weight are included. You can make CNC machining parts out of a variety of materials, including the following:
Plastics Material
Plastics are an important raw material for the fabrication of CNC machining parts. They are corrosion-resistant and lightweight, which is essential. And, because many sectors, such as automotive and electronics, demand flexibility in their components, plastic is a crucial component for many enterprises. The most widely used polymers are PVC, Nylon, POM, PEEK, ABS, and PTFE.
Metals and alloys
Metals and alloys are the most widely used materials for CNC machining parts. This is due to the wide range of applications that they are used in many industries. They have high mechanical strength, long life time, low initial cost, and no MOQ requirement, and good surface finish. The most commonly used metals for this purpose are titanium, copper, brass, zinc alloy, magnesium, stainless steel, 302, 304, and aluminium.
How to Choose the Best CNC Machining Parts?
To ensure that CNC machining components last as long as possible, it is important to think about all of factors when you use CNC machining parts, those include material of CNC products, surface finish of CNC machined parts, hardness of CNC parts. Below are some key points you may need to think about in advance:
Heat Resistance
The heat resistance of a substance determines directly whether it can maintain high temperatures without warping. The material is heated using several techniques across the manufacturing process. For instance, it is heated during the cutting and milling operations, which, should the material be not heat-resistant, can cause further thermal expansion or breaking.
Electrical Conductivity
Electrical conductivity can be used to determine whether a material can conduct electricity. CNC machined components with high conductivity may readily and effectively distribute heat. During the CNC machining process, this not only helps the CNC machined product but also keeps it from becoming distorted. Copper, brass and aluminium are used in this scenario due of their heat dissipation properties.
Surface Finish
The final and most important step for the CNC machined product is the surface finish. As a result, it affects both the performance and appearance of the CNC components. For example, a component with a rough surface will experience more friction and wear. In contrast, cnc machining components with a smooth surface finish will function more smoothly, encounter less friction, and perform better. Surface finishing can be achieved in a variety of techniques, including powder coating, anodizing, electronic plating, sand blasting, and painting.
Advantages & Disadvantages of CNC Machined products
The applications of CNC machining parts are quite varied and can be found in a variety of industries. However, along with the benefits come a few drawbacks as well. The following is a list of some of the benefits and drawbacks associated with CNC machined parts.
Advantages of CNC machining parts
Strength of CNC machining parts
The durability of the components that are being manufactured is determined by their strength. In addition, CNC machining components are not only tough but also highly robust. As a result, you can put your complete faith in this aspect of them. The absence of any internal stresses in them is the reason for this. When it comes to the components that are produced by other processes, however, the situation is different. Furthermore, due to the fact that these components are made from solid blocks, they are very sturdy.
Alterations of CNC machining
Before a product is created, it is critical to make any necessary design changes. You have the ability to make as many changes as necessary. However, this depends on the CAD design you made at the start of the procedure. What you need to do is create the designs again, but this time with the parameters altered. As a result, changes to this procedure are straightforward to adopt. In contrast, no other process behaves in this way.
Quality of machining parts
The most crucial consideration is the type of products being created. Furthermore, the properties such as tight tolerances, precision, smooth surface finishes, and quality standards contribute to their ability to last for an extended period of time. This is why they are used in so many different sectors.
CNC machining components have several advantages, one of which is that they do not require a minimum order quantity (MOQ). This means that a small batch of these components can be produced at a much lower cost. This cannot be achieved using any other manufacturing process.
CNC machining parts have several advantages over other types of components that set them apart from their competition.
Disadvantages
Tool Presetting
When performing CNC machining, the tool must be adjusted such that the cutting tip is in the proper position. As a result, each instrument must be installed in the appropriate area. A single inaccuracy made right now has the ability to disrupt the entire cutting process. The cutting technique begins by measuring the tip location, which is then entered into the software to initiate the cutting process. One downside of CNC machined parts may be the need for tool presetting.
Visibility and Access

The CNC tools are totally encased to protect the operators from moving machine components encountered throughout the CNC part manufacturing process. This creates a barrier that prohibits visibility and access to the component in question. Even in the event of a catastrophic crisis, little can be done to affect the outcome. This is yet another downside to adopting CNC machining.
In terms of quality, standards, and longevity, CNC machined parts outperform alternative techniques of manufacturing. This is true even if CNC machined components have both advantages and downsides.
Conclusión
The manufacturing of CNC machining parts is a challenging procedure. However, once made, they can continue to serve for an extended period of time. Their strength, durability, and tolerances have made them game changers in a variety of industries.
Fortuna is your one-stop shop for CNC machining, 2D and 3D printing, and many other services. Today, take advantage of all the benefits that CNC machined components provide.
GC mould is one of top 10 aluminum die casting manufacturers in China, that offer custom aluminum die casting, zinc die casting, CNC machining and surface finish, if you are looking for CNC machining parts, welcome to contact us.